PPUASB三相分離器 塑料UASB三相分離器 塑料模塊三相分離器 厭氧罐三相分離器 IC三相分離器 三相分離器模塊 厭氧三相反應器 聚丙烯PP三相分離器
三相分離器鋪設中管槽增設:提升效能與穩(wěn)定性的關鍵舉措
在石油、化工、污水處理等眾多涉及多相流分離的工業(yè)***域中,三相分離器扮演著至關重要的角色。其高效精準地分離氣、液、固三相物質(zhì)的能力,直接關系到整個生產(chǎn)流程的連續(xù)性、產(chǎn)品質(zhì)量以及設備運行的穩(wěn)定性。而在三相分離器的鋪設過程中,增加管槽這一操作,雖看似細微,實則蘊含著對系統(tǒng)性能全方位***化的深意,從流體動力學原理、設備耐久性到維護便捷性等多方面有著不可忽視的影響。
一、三相分離器基本原理與作用復盤
三相分離器依據(jù)各相物質(zhì)的密度差異,利用重力沉降、離心力分離以及聚結等原理,促使氣相、液相和固相在***定腔室結構內(nèi)分層。氣相憑借密度小向上流動,經(jīng)***部出口排出;液相居于中間層,通過***定溢流裝置導出;固相則因重力沉淀至底部,定期或連續(xù)排放。這一過程看似簡單,實則對內(nèi)部流場分布、各相停留時間以及相間干擾等因素極為敏感,任何細微的結構變動都可能牽一發(fā)而動全身,影響分離效率與效果。
二、鋪設時增加管槽的必要性剖析
(一)***化流體流向與分布
1. 引導氣相順暢排出
在三相分離器氣相出口附近增設管槽,能夠為高速上升的氣相提供明確且低阻的通道。管槽的幾何形狀經(jīng)過精心設計,如漸縮式結構,可使氣相在加速流出過程中保持平穩(wěn)的流速分布,避免局部渦流與紊流的產(chǎn)生。渦流不僅會消耗氣相動能,降低排氣效率,還可能攜帶液滴或固顆粒,導致分離不徹底,引發(fā)后續(xù)設備堵塞或腐蝕問題。例如在天然氣處理工廠中,氣相夾帶液滴進入壓縮機,會造成葉片磨損、閥門卡澀等故障,影響設備壽命與運行可靠性。
管槽內(nèi)壁的光滑度處理至關重要,采用***殊涂層或拋光工藝,能進一步減小氣體流動的摩擦阻力。據(jù)實際工程測算,內(nèi)壁粗糙度從 Ra 50μm 降低至 Ra 10μm,氣相流動壓降可減少約 15%,顯著提升了排氣能力,保障分離器在高負荷工況下仍能維持穩(wěn)定的氣相分離效果。
2. 助力液相均勻?qū)С?/div>
對于液相而言,增加的管槽可以作為緩沖與均流區(qū)域。當液相從三相混合區(qū)流入管槽時,其湍流程度逐漸衰減,流速趨于均勻。管槽的合理布局,如環(huán)形或多分支狀設計,能確保來自不同方位的液相匯合后平穩(wěn)地向出口流動,避免因流速差異過***形成偏流現(xiàn)象。偏流會使液相在局部區(qū)域滯留,增加液相中固體雜質(zhì)沉積的風險,進而堵塞液相出口管道,擾亂分離器正常運行秩序。
管槽還具備一定的液位調(diào)節(jié)功能。通過在管槽***定位置設置溢流堰,可根據(jù)分離器內(nèi)液相高度自動調(diào)整液相流出速率。當進液量突然增***時,溢流堰能有效攔截過多液體,使液位在合理范圍內(nèi)波動,防止液相淹沒氣相出口或涌入固相沉積區(qū),保證三相分離的界限清晰,提升分離純度。
3. 輔助固相有序沉降
固相顆粒在三相分離器底部的沉降過程易受液相流動干擾,增設管槽可對液相流向進行梳理,減少液相橫向沖刷固相沉積層的力量。管槽圍繞固相沉降區(qū)外圍布置,如同一道“護城河”,引導液相沿管槽流向出口,而非直接沖擊固相堆積處。這使得固相顆粒能在相對安靜的環(huán)境中沉降聚集,提高固相捕集效率,尤其對于細小顆粒,避免其因液相攪動而再次懸浮,隨液相流出分離器,造成后續(xù)管道磨損與環(huán)境污染。
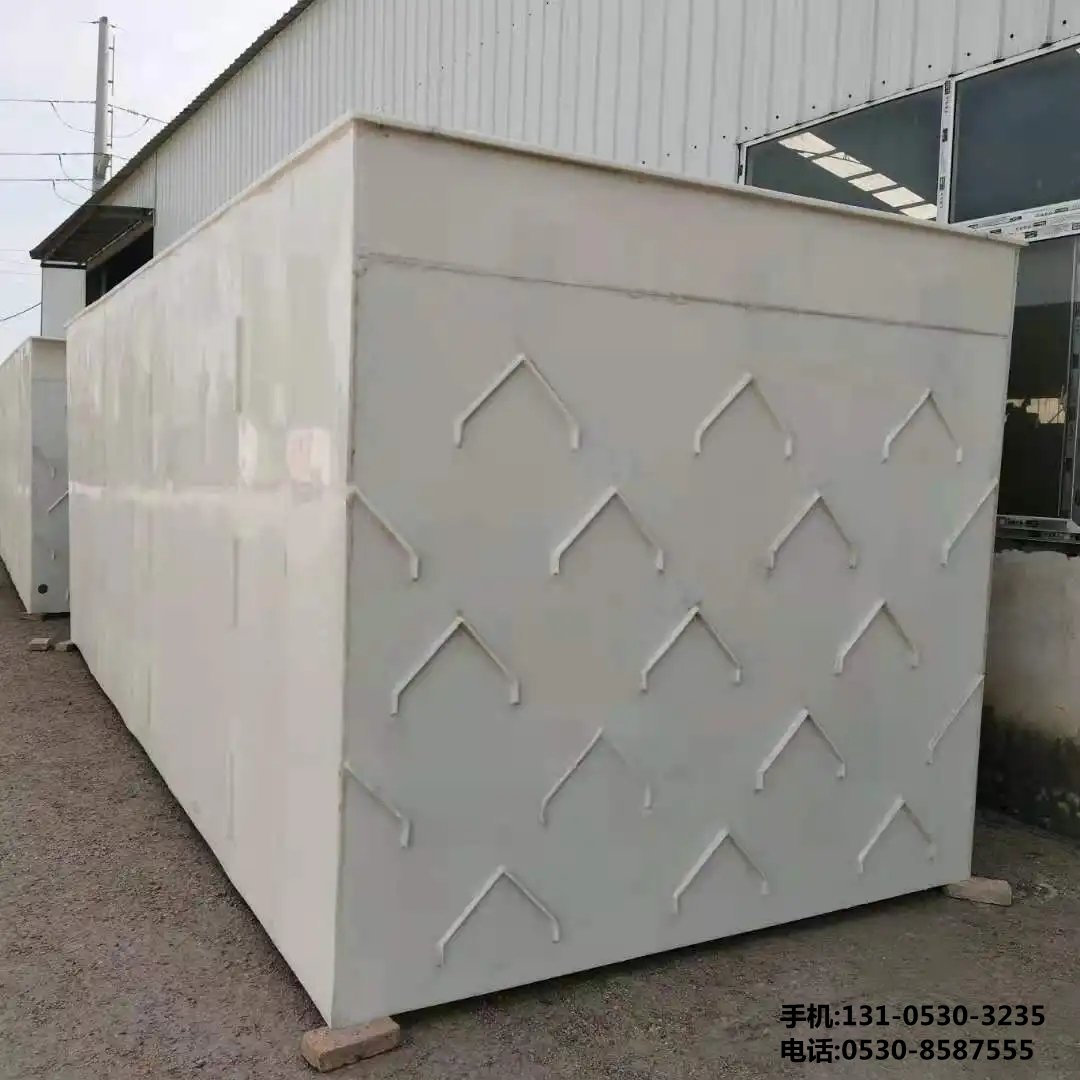
(二)強化設備結構穩(wěn)定性
1. 分散應力集中點
三相分離器在運行過程中,承受著內(nèi)部壓力、溫度變化以及介質(zhì)腐蝕等多種外力作用。管槽的增加相當于在設備殼體上設置了多個應力緩沖區(qū)。當分離器內(nèi)部壓力波動時,管槽能夠分擔部分殼體所受應力,將集中的應力分布到更***的面積上,降低殼體局部應力水平。例如在高壓原油處理場景中,壓力驟變可能導致殼體焊縫處產(chǎn)生裂紋,而管槽的存在可使該區(qū)域應力強度降低 30% 50%,顯著延長設備疲勞壽命,減少因結構失效引發(fā)的泄漏事故風險。
2. 增強抗震與抗沖擊能力
在一些戶外或地震多發(fā)地區(qū)的工業(yè)裝置中,設備的抗震性能尤為重要。管槽與分離器主體焊接成整體,增加了設備的整體剛性。當遭遇地震波或外部機械沖擊時,管槽能夠吸收并分散能量,像一個個“減震梁”,減輕設備晃動幅度,保護內(nèi)部精密分離構件免受損壞。同時,對于內(nèi)部可能產(chǎn)生的水錘、氣錘等瞬態(tài)沖擊現(xiàn)象,管槽也能起到一定的緩沖作用,通過改變沖擊波的傳播路徑,削弱其對設備關鍵部位的破壞力,確保三相分離器在惡劣工況下的安全穩(wěn)定運行。
(三)便于安裝與后期維護
1. 簡化安裝流程
在三相分離器的現(xiàn)場安裝過程中,增加管槽后可將原本復雜的管路連接工作部分轉(zhuǎn)移到管槽預制環(huán)節(jié)。管槽在工廠內(nèi)根據(jù)設計圖紙***加工成型,包括開孔位置、坡度設定等細節(jié)都能得到******控制。運至現(xiàn)場后,只需將管槽與分離器主體進行有限幾點的焊接或法蘭連接,即可完成***部分流體導向結構的安裝,******縮短了施工周期。相較于傳統(tǒng)現(xiàn)場逐根管路拼接的方式,減少了高空作業(yè)、狹窄空間作業(yè)的難度與工作量,提高了安裝效率與質(zhì)量,降低了施工安全風險。
2. 利于設備檢修與更換部件
管槽的設計充分考慮了后期維護便利性。當需要對分離器內(nèi)部某一部件,如液相出口閥、氣相除霧器等進行檢修或更換時,管槽可作為便捷的操作通道。維修人員無需***面積拆卸設備殼體,只需打開管槽上預留的檢修口,便能深入內(nèi)部進行作業(yè)。而且,管槽內(nèi)通??臻g較為寬敞,便于工具使用與零部件進出,減少了維修時間與成本。此外,若管槽某段因長期腐蝕或磨損需要更換,由于其模塊化設計,可單***拆卸替換,不影響分離器整體結構的完整性,實現(xiàn)了設備全生命周期維護的高效性與經(jīng)濟性。
三、管槽設計與實施要點
(一)材質(zhì)選擇
管槽材質(zhì)需依據(jù)三相分離器內(nèi)介質(zhì)***性而定。若處理的是酸性油氣混合物,如含硫化氫的天然氣,應選用耐腐蝕性極強的不銹鋼材質(zhì),如雙相不銹鋼 2205 或超級奧氏體不銹鋼 904L,它們對酸性環(huán)境具有******的耐受性,能防止管槽在短時間內(nèi)被腐蝕穿孔。對于高溫工況,如熱電廠的蒸汽 水 固體顆粒三相分離,碳鋼材質(zhì)搭配耐高溫涂層可能是經(jīng)濟實惠的選擇,既能承受高溫熱應力,又能抵御一定程度的蒸汽腐蝕。在一些化學性質(zhì)溫和的工況下,普通碳鋼或鋁合金管槽也可滿足要求,但同樣要考慮長期的抗老化與耐磨性能。
(二)尺寸與形狀規(guī)劃
1. 管槽尺寸
管槽的寬度與高度要適配三相分離器內(nèi)部流體流量與流速需求。一般來說,氣相管槽寬度應根據(jù)氣相***流量計算,確保在滿負荷運行時氣速不超過臨界值,避免氣相攜帶液相過多。液相管槽截面積則要考慮液相正常處理量及一定余量,防止液位過高溢出。以某日處理量為 1000 立方米的小型污水處理三相分離器為例,氣相管槽寬度設計在 200 300mm 左右,液相管槽高度約 150 200mm,既能滿足日常運行,又有一定的彈性應對流量波動。
管槽長度依據(jù)分離器內(nèi)部結構布局確定,要保證流體在管槽內(nèi)有足夠長的穩(wěn)定流動距離,以充分完成均流、緩沖等作用。同時,需考慮管槽與其他內(nèi)部構件的間距,避免相互干擾,一般預留 100 200mm 的空間用于安裝與維護操作。
2. 形狀設計
氣相管槽多采用漸縮形或矩形直角彎頭結構,漸縮部分能使氣相平穩(wěn)加速,減少能量損失;直角彎頭則確保氣流方向準確改變,防止氣流偏斜撞擊管壁。液相管槽常設計為環(huán)形或 U 形,環(huán)形管槽利于各方向來液均勻匯聚,U 形管槽可提供一定的液封高度,防止氣相竄入液相出口。固相沉降區(qū)周邊管槽可設計為斜坡狀,朝向固相排放口,助力固相滑入收集裝置。
(三)連接與密封方式
管槽與三相分離器主體的連接方式關乎設備整體密封性與強度。焊接是常見且可靠的連接手段,采用氬弧焊或埋弧焊等工藝,保證焊縫質(zhì)量,防止泄漏。對于一些需要頻繁拆卸檢修的部位,如管槽上的法蘭接口,應選用合適的法蘭標準,如 PN16 或 PN25 的平面法蘭,搭配耐腐蝕密封墊片,如聚四氟乙烯墊片或金屬纏繞墊片,既能保證密封效果,又便于安裝與更換。在管槽自身拼接處,同樣要做***密封處理,采用密封膠或焊接加強筋等措施,確保管槽內(nèi)部流體無滲漏隱患,維持三相分離器******的工作環(huán)境。
四、實際應用案例與效益分析
(一)案例呈現(xiàn)
在某***型海上石油平臺,原油經(jīng)井口采出后含有***量伴生氣、砂粒以及水分,需通過三相分離器進行初步處理。起初,分離器未設管槽,運行時頻繁出現(xiàn)氣相帶液嚴重、液相出口堵塞以及設備振動過***等問題。后對分離器進行改造,在氣、液、固三相出口附近及關鍵流道處增加管槽。改造后,氣相帶液率從原來的 15%降低至 3%以內(nèi),液相出口因固體雜質(zhì)堆積造成的堵塞故障率下降了 80%,設備振動幅度減小約 40%,有效保障了石油平臺原油處理系統(tǒng)的穩(wěn)定運行,提高了原油外輸質(zhì)量與生產(chǎn)效率。
(二)效益評估
1. 經(jīng)濟效益
從運行成本角度看,***化后的三相分離器因分離效率提升,減少了后續(xù)原油脫水、天然氣凈化等工序的負荷,降低了能源消耗與化學藥劑用量。據(jù)統(tǒng)計,每年可節(jié)省電費約 20 萬元、脫水劑費用 15 萬元。同時,設備故障率降低意味著維修次數(shù)減少,維修人工與配件成本每年節(jié)約近 30 萬元,***幅提升了平臺的經(jīng)濟收益。
2. 安全與環(huán)保效益
在安全方面,管槽增設使設備結構更穩(wěn)固,降低了因分離器失效引發(fā)原油泄漏、爆炸等重***安全事故的風險。從環(huán)保角度出發(fā),氣相帶液減少意味著更少的原油揮發(fā)到***氣中,液相出口堵塞緩解避免了含油污水違規(guī)排放,有效保護了海洋生態(tài)環(huán)境,契合現(xiàn)代工業(yè)綠色可持續(xù)發(fā)展理念,提升了企業(yè)社會形象與合規(guī)性。
五、結論與展望
三相分離器鋪設中增加管槽***非簡單的結構改***,而是基于深刻理解多相流***性與設備運行需求的關鍵***化策略。它在流體動力學***化、設備結構強化以及維護便利性提升等多方面成效顯著,為三相分離器乃至整個工業(yè)生產(chǎn)系統(tǒng)的高效、穩(wěn)定、安全運行筑牢根基。隨著工業(yè) 4.0 時代的到來,未來管槽設計有望融入更多智能化元素,如內(nèi)置傳感器監(jiān)測管槽內(nèi)流體狀態(tài)、利用物聯(lián)網(wǎng)技術實現(xiàn)遠程運維指導等,進一步提升三相分離器的性能與管理水準,持續(xù)推動相關工業(yè)***域向更高質(zhì)量方向發(fā)展。
返回:技術方案